The road to electric vehicles with lower sticker prices than gas cars – battery costs explained
- Written by Venkat Viswanathan, Associate Professor of Mechanical Engineering, Carnegie Mellon University
Electric vehicle sales[1] have grown exponentially in recent years, accompanied by dropping prices. However, adoption of EVs remains limited by their higher sticker price[2] relative to comparable gas vehicles, even though overall cost of ownership for EVs is lower[3].
EVs and internal combustion engine vehicles are likely to reach sticker price parity sometime in the next decade. The timing hinges on one crucial factor: battery cost. An EV’s battery pack accounts for about a quarter of total vehicle cost[4], making it the most important factor in the sales price.
Battery pack prices have been falling fast. A typical EV battery pack stores 10-100 kilowatt hours (kWh) of electricity. For example, the Mitsubishi i-MIEV has a battery capacity of 16 kWh and a range of 62 miles, and the Tesla model S has a battery capacity of 100 kWh and a range of 400 miles. In 2010, the price of an EV battery pack was over $1,000 per kWh. That fell to $150 per kWh in 2019[5]. The challenge for the automotive industry is figuring out how to drive the cost down further.
The Department of Energy goal[6] for the industry is to reduce the price of battery packs to less than $100/kWh and ultimately to about $80/kWh. At these battery price points, the sticker price of an EV is likely to be lower than that of a comparable combustion engine vehicle.
[Deep knowledge, daily. Sign up for The Conversation’s newsletter[7].]
Forecasting when that price crossover will occur requires models that account for the cost variables: design, materials, labor, manufacturing capacity and demand. These models also show where researchers and manufacturers are focusing their efforts to reduce battery costs. Our group[8] at Carnegie Mellon University has developed a model of battery costs that accounts for all aspects of EV battery manufacturing.
From the bottom up
Models used for analyzing battery costs are classified either as “top down” or “bottom up.” Top-down models predict cost based primarily on demand and time. One popular top-down model that can forecast battery cost[9] is Wright’s law, which predicts that costs go down as more units are produced. Economies of scale and the experience an industry acquires over time drive down costs.
Wright’s law is generic. It works across all technologies[10], which makes it possible to predict battery cost declines based on solar panel cost declines[11]. However, Wright’s law - like other top-down models - doesn’t allow for the analysis of the sources of the cost declines. For that, a bottom-up model is required.
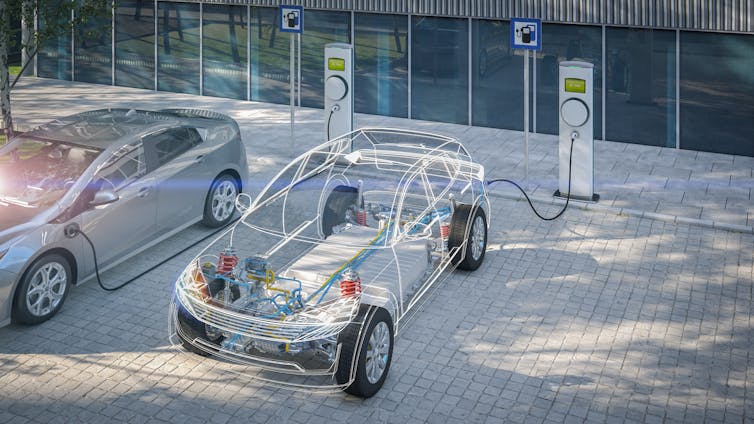
To build a bottom-up cost model, it’s important to understand what goes into making a battery. Lithium-ion batteries consist of a positive electrode, the cathode, a negative electrode, the anode and an electrolyte, as well as auxiliary components such as terminals and casing.
Each component has a cost associated with its materials, manufacturing, assembly, expenses related to factory maintenance, and overhead costs. For EVs, batteries also need to be integrated into small groups of cells, or modules, which are then combined into packs.
Our open source, bottom-up battery cost model[13] follows the same structure as the battery manufacturing process itself. The model uses inputs to the battery manufacturing process as inputs to the model, including battery design specifications, commodity and labor prices, capital investment requirements like manufacturing plants and equipment, overhead rates and manufacturing volume to account for economies of scale. It uses these inputs to calculate manufacturing costs, material costs and overhead costs, and those costs are summed to arrive at the final cost.
Cost-cutting opportunities
Using our bottom-up cost model, we can break down the contributions of each part of the battery to the total battery cost and use those insights to analyze the impact of battery innovations on EV cost. Materials make up the largest portion of the total battery cost, around 50%. The cathode accounts for around 43% of the materials cost, and other cell materials account for around 36%.
Improvements in cathode materials are the most important innovations, because the cathode is the largest component of battery cost. This drives strong interest in commodity prices[14].
The most common cathode materials for electric vehicles are nickel cobalt aluminum oxide used in Tesla vehicles[15], nickel manganese cobalt oxide used in most other electric vehicles[16], and lithium iron phosphate used in most electric buses[17].
Nickel cobalt aluminum oxide has the lowest cost-per-energy-content and highest energy-per-unit-mass, or specific energy, of these three materials. A low cost per unit of energy results from a high specific energy because fewer cells are needed to build a battery pack. This results in a lower cost for other cell materials. Cobalt is the most expensive material within the cathode, so formulations of these materials with less cobalt typically lead to cheaper batteries.
Inactive cell materials such as tabs and containers account for roughly 36% of the total cell materials cost. These other cell materials do not add energy content to the battery. Therefore, reducing inactive materials reduces the weight and size of battery cells without reducing energy content. This drives interest in improving cell design with innovations such as tabless batteries[18] like those being teased by Tesla.
The battery pack cost also decreases significantly with an increase in the number of cells manufacturers produce annually. As more EV battery factories come on-line[19], economies of scale and further improvement in battery manufacturing and design should lead to further cost declines.
Road to price-parity
Predicting a timeline for price parity with ICE vehicles requires forecasting a future trajectory of battery costs. We estimate that reduction in raw material costs, improvements in performance and learning by manufacturing together are likely to lead to batteries with pack costs below $80/kWh by 2025.
Assuming batteries represent a quarter of the EV cost[20], a 100 kWh battery pack at $75 per kilowatt hour yields a cost of about $30,000. This should result in EV sticker prices that are lower than the sticker prices for comparable models of gas-powered cars.
Abhinav Misalkar contributed to this article while he was a graduate student at Carnegie Mellon University.
References
- ^ Electric vehicle sales (www.woodmac.com)
- ^ higher sticker price (www.digitaltrends.com)
- ^ overall cost of ownership for EVs is lower (cleantechnica.com)
- ^ a quarter of total vehicle cost (theicct.org)
- ^ $150 per kWh in 2019 (about.bnef.com)
- ^ Department of Energy goal (www.energy.gov)
- ^ Sign up for The Conversation’s newsletter (theconversation.com)
- ^ Our group (www.andrew.cmu.edu)
- ^ forecast battery cost (ark-invest.com)
- ^ across all technologies (doi.org)
- ^ battery cost declines based on solar panel cost declines (www.vox.com)
- ^ Sven Loeffler/iStock via Getty Images (www.gettyimages.com)
- ^ open source, bottom-up battery cost model (github.com)
- ^ interest in commodity prices (www.mckinsey.com)
- ^ used in Tesla vehicles (www.reuters.com)
- ^ most other electric vehicles (batteryuniversity.com)
- ^ used in most electric buses (www.sustainable-bus.com)
- ^ tabless batteries (www.popularmechanics.com)
- ^ come on-line (www.benchmarkminerals.com)
- ^ a quarter of the EV cost (about.bnef.com)
Authors: Venkat Viswanathan, Associate Professor of Mechanical Engineering, Carnegie Mellon University