Scientists are developing greener plastics – the bigger challenge is moving them from lab to market
- Written by Richard Gross, Professor of Chemistry, Rensselaer Polytechnic Institute
Synthetic plastics have made many aspect of modern life cheaper, safer and more convenient. However, we have failed to figure out how to get rid of them after we use them.
Unlike other forms of trash, such as food and paper, most synthetic plastics cannot be easily degraded by live microorganisms or through chemical processes. As a result, a growing plastic waste crisis threatens the health of our planet. It is embodied by the Great Pacific Garbage Patch[1] – a massive zone of floating plastic trash, three times the size of France[2], stretching between California and Hawaii. Scientists have estimated that if current trends continue, the mass of plastics in the ocean will equal the mass of fish by 2050[3]. Making plastics from petroleum also increases carbon dioxide levels in the atmosphere, contributing to climate change.
Much of my work[4] has been dedicated to finding sustainable ways to make and break down plastics[5]. My lab and others are making progress on both fronts. But these new alternatives have to compete with synthetic plastics that have established infrastructures and optimized processes. Without supportive government policies, innovative plastic alternatives will have trouble crossing the so-called “valley of death[6]” from the lab to the market.
From wood and silk to nylon and plexiglass
All plastics consist of polymers[7] – large molecules that contain many small units, or monomers, joined together to form long chains, much like strings of beads. The chemical structure of the beads and the bonds that join them together determine polymers’ properties. Some polymers form materials that are hard and tough, like glass and epoxies. Others, such as rubber, can bend and stretch.
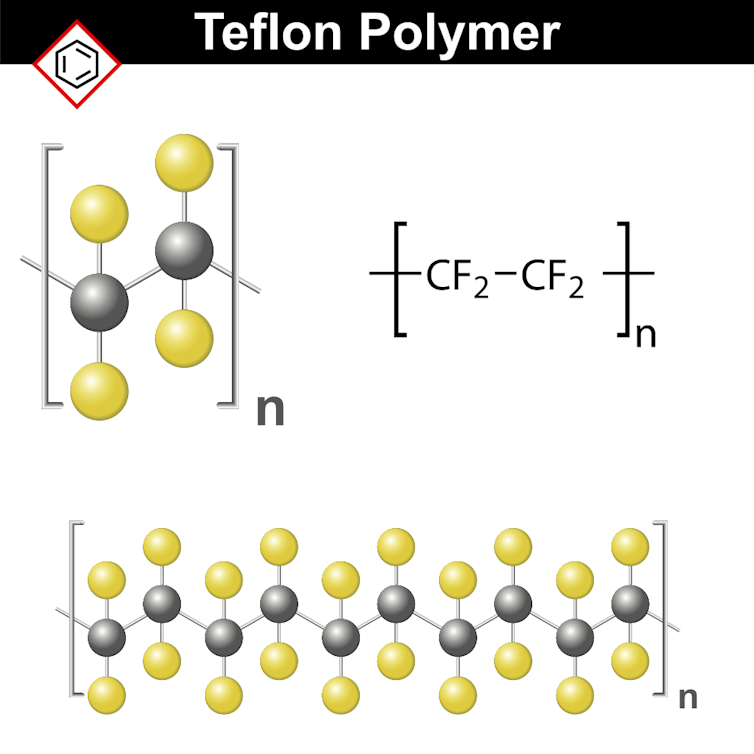
For centuries humans have made products out of polymers from natural sources, such as silk, cotton, wood and wool. After use, these natural plastics are easily degraded by microorganisms.
Synthetic polymers derived from oil were developed starting in the 1930s, when new material innovations were desperately needed to support Allied troops in World War II. For example, nylon, invented in 1935[9], replaced silk in parachutes and other gear. And poly(methyl methacrylate), known as Plexiglas[10], substituted for glass in aircraft windows. At that time, there was little consideration of whether or how these materials would be reused.
Modern synthetic plastics can be grouped into two main families: Thermoplastics, which soften on heating and then harden again on cooling, and thermosets, which never soften once they have been molded. Some of the most common high-volume synthetic polymers include polyethylene, used to make film wraps and plastic bags; polypropylene, used to form reusable containers and packaging; and polyethylene terephthalate, or PET, used in clothes, carpets and clear plastic beverage bottles.
Recycling challenges
Today only about 10 percent[11] of discarded plastic in the United States is recycled. Processors need an input stream of non-contaminated or pure plastic, but waste plastic often contains impurities, such as residual food.
Batches of disposed plastic products also may include multiple resin types, and often are not consistent in color, shape, transparency, weight, density or size. This makes it hard for recycling facilities to sort them by type[12].
Melting down and reforming mixed plastic wastes creates recycled materials that are inferior in performance to virgin material. For this reason, many people refer to plastic recycling as “downcycling[13].”
As most consumers know, many plastic goods are stamped with a code that indicates the type of resin they are made from, numbered one through seven, inside a triangle formed by three arrows. These codes were developed in the 1980s by the Society of the Plastics Industry[14], and are intended to indicate whether and how to recycle those products.
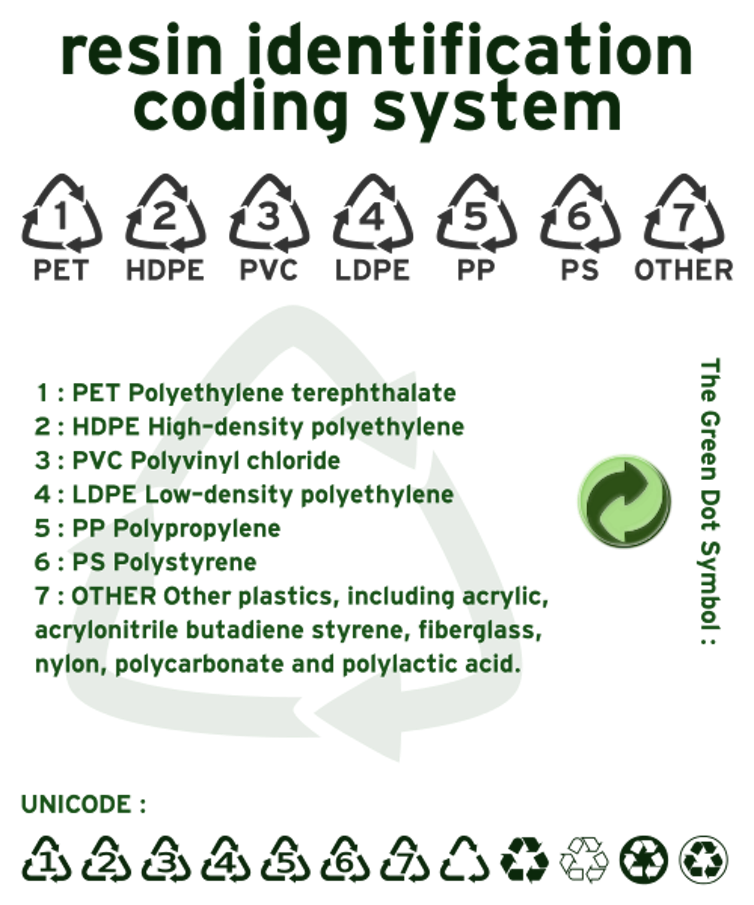
References
- ^ Great Pacific Garbage Patch (marinedebris.noaa.gov)
- ^ three times the size of France (www.cnn.com)
- ^ equal the mass of fish by 2050 (www.ellenmacarthurfoundation.org)
- ^ my work (scholar.google.com)
- ^ sustainable ways to make and break down plastics (global.oup.com)
- ^ valley of death (www.greentechmedia.com)
- ^ polymers (plastics.americanchemistry.com)
- ^ Chromatos (www.shutterstock.com)
- ^ nylon, invented in 1935 (www.acs.org)
- ^ Plexiglas (www.eplastics.com)
- ^ only about 10 percent (www.epa.gov)
- ^ sort them by type (www.plasticsrecycling.org)
- ^ downcycling (www.greenhome.com)
- ^ Society of the Plastics Industry (plastics.americanchemistry.com)
- ^ Filtre (commons.wikimedia.org)
- ^ recycling rates in 2015 (www.epa.gov)
- ^ Germany (doi.org)
- ^ composts organic wastes from homes and businesses (www.cnbc.com)
- ^ converting carbon from plant cell walls (lignocellulosics) into monomers (arxiv.org)
- ^ converts them to a polyester (dx.doi.org)
- ^ fully degraded by microorganisms in composting systems (dx.doi.org)
- ^ digest polystyrene (dx.doi.org)
- ^ can form and break (dx.doi.org)
- ^ polylactic acid (dx.doi.org)
- ^ compost bags, food containers, cups and disposable tableware (www.environmentalleader.com)
- ^ European Union (ec.europa.eu)
- ^ Canada (biomassmagazine.com)
Authors: Richard Gross, Professor of Chemistry, Rensselaer Polytechnic Institute