Fast fashion still comes with deadly risks, 10 years after the Rana Plaza disaster – the industry's many moving pieces make it easy to cut corners
- Written by Ravi Anupindi, Professor of Technology and Operations, University of Michigan
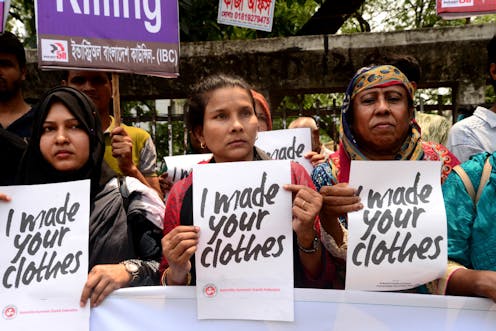
On April 24, 2013, a multistory garment factory complex in Bangladesh called Rana Plaza collapsed, killing more than 1,000 workers[1] and injuring another 2,500. It remains the worst accident in the history of the apparel industry and one of the deadliest industrial accidents in the world.
Several factories inside the complex produced apparel for Western brands[2], including Benetton, Primark and Walmart, shining a spotlight on the unsafe conditions in which a sizable portion of Americans’ cheap clothing is produced. The humanitarian tragedy hit home as wealthy nations’ shoppers wrestled with their own complicity and called for reforms – but a decade later, progress is still patchy.
As a professor of operations and supply chain management[3], I believe it is important to understand how the complex and fragmented supply chains that are the norm in the clothing industry create conditions where unsafe conditions and abuse can flourish – and make it difficult to assign responsibility for reforms.
Shamed into action?
Rana Plaza was not the first garment industry accident in Bangladesh[4]. While the government had stringent building codes “on the books,” they were rarely enforced[5]. Most workers lacked the information and power to demand safe working conditions.
Yet the fact that the Rana Plaza collapse was not only a humanitarian crisis, but a public relations crisis, prompted swift action by international organizations and Western brands and clothing retailers. A campaign for full and fair compensation[6] for families of victims was launched immediately, facilitated by the International Labor Organization[7], a U.N. agency. Within a few months, two initiatives were designed to bring garment factories in Bangladesh up to international standards: the European-led Accord for Fire and Building Safety[8], and the American-led Alliance for Bangladesh Worker Safety[9].
While the two initiatives differed in some important ways, both shared the common goal: to improve building and fire safety by leveraging the purchasing power of the member companies. In other words, Western brands would insist that production partners get up to standard or take their business elsewhere.
Altogether, the two agreements covered about 2,300 supplier factories. The coalitions conducted factory inspections to identify structural and electrical deficiencies and developed plans for factories to make improvements. The initiatives also laid the groundwork to form worker safety committees and to train workers[11] to recognize, solve and prevent health and safety issues. Member companies set aside funds for inspections and worker training, negotiated commercial terms[12] and facilitated low-cost loans[13] for factory improvements.
Both were five-year agreements: the Alliance was sunsetted in 2018[14], whereas the Accord operated for a few more years before handing operations over to the locally created Readymade Sustainability Council[15] in June 2020.
The record since
The onus and expense of making these improvements, however, were largely to be borne by the suppliers – a substantial financial burden for many factories, especially considering the low cost and slim profit margins of the clothes they were producing.
Under the Alliance and the Accord, thousands of factories were inspected for building and fire safety, identifying problems such as lack of fire extinguishers and sprinkler systems, improper fire exits, faulty wiring and structural issues. At the end of five years, both initiatives reported that 85%-88% of safety issues were remediated[16]. Around half of the factories completed more than 90% of initial remediation, while over 260 of the original 2,300 factories under the initiatives were suspended from contracting with member companies.
In addition, more than 5,000 beneficiaries, including injured workers and dependents of victims, were compensated through the Rana Plaza Arrangement[17], receiving an average of about US$6,500.
Overall, I believe that these initiatives have been successful in bringing safety issues to the forefront. In terms of infrastructure improvements, however, while there has been decent progress, much still needs to be done; for example, the initiatives covered just about one-third of all the garment factories in Bangladesh[18]. Importantly, neither addressed company sourcing practices.
Clothes yesterday and today
To understand why so much apparel manufacturing takes place in substandard conditions, we need to understand the underlying economic forces: extensive outsourcing to countries with low wages in the quest to meet demand for more – and cheaper – clothing to sell to customers in the West.
In the 1960s, the average American family spent 10% of its income on clothing[20], buying 25 pieces of apparel – almost all of it made in the United States. Fifty years later, around the time of the Rana Plaza disaster, the average household was spending only about 3.5% of its income on clothing – but buying three times as many items, 98% of which were imported.
Over these decades, low-income countries in Asia and Latin America started producing more garments and textiles. Apparel production is labor-intensive, meaning these countries’ lower wages were a huge attraction to brands and retailers, who gradually started shifting their sourcing.
On a $30 shirt, for example, a typical retailer markup is close to 60%. The factory makes a profit of $1.15, and the worker makes barely 18 cents[21]. Were a similar shirt produced in the U.S., labor costs would be closer to $10[22].
As labor costs rose in China, Bangladesh became a very appealing alternative[23]. Garment exports now account for 82% of the country’s export total[24], and the industry employs 4 million people[25], about 58% of whom are women.
The growth of this sector has reduced poverty[26] significantly and also empowered women[27]. To meet the rapid growth of the apparel industry, however, many buildings were converted to factories as quickly as possible, often without requisite permits.
Everyone and no one
A common way that foreign companies source products from low-cost countries like Bangladesh is through intermediaries or agents. For example, when a brand places a large order with an authorized factory, the factory in turn may subcontract part of the production to smaller factories[28], often without informing the brand.
This highly competitive environment, with people at each step of the process looking for the lowest price and no guarantee of longer-term relationships, gives suppliers incentives to cut corners – particularly when under extreme pressure to deliver on time. This can translate into exploitative labor practices[29] or unsafe conditions that violate local laws, but enforcement capacity is weak.
In their constant quest for lower prices, buyers may turn a blind eye to these practices. The supply chain’s opaqueness, especially when brands do not source directly, makes it difficult to investigate and remediate these practices. Since the 1990s, international scrutiny of labor conditions[31] has grown, but reform efforts largely ignored building and fire safety, the prime reason for the Rana Plaza collapse. Because multiple buyers would often use the same factory, no single buyer felt obligated to invest in the supplier to ensure better conditions.
Garments traverse a complex global supply network by the time they reach stores thousands of miles away. Workers are caught in this web, exploited by factory management that is seldom held responsible by governments either unwilling or unable to enforce laws[32]. Western brands escape the scrutiny of their governments by outsourcing production to low-cost countries and absolve themselves of direct responsibility. And consumers, eager for a bargain, shop for the lowest price.
This complex system makes it hard to assign ethical responsibility, because everyone, and therefore no one, is guilty.
References
- ^ killing more than 1,000 workers (www.bbc.com)
- ^ produced apparel for Western brands (www.forbes.com)
- ^ a professor of operations and supply chain management (michiganross.umich.edu)
- ^ not the first garment industry accident in Bangladesh (www.dhakatribune.com)
- ^ they were rarely enforced (ces.ulab.edu.bd)
- ^ full and fair compensation (ranaplaza-arrangement.org)
- ^ the International Labor Organization (www.ilo.org)
- ^ Accord for Fire and Building Safety (bangladeshaccord.org)
- ^ Alliance for Bangladesh Worker Safety (www.business-humanrights.org)
- ^ AP Photo/Wong Maye-E (newsroom.ap.org)
- ^ and to train workers (iosh.com)
- ^ negotiated commercial terms (cleanclothes.org)
- ^ facilitated low-cost loans (www.wsj.com)
- ^ was sunsetted in 2018 (www.business-humanrights.org)
- ^ Readymade Sustainability Council (www.business-humanrights.org)
- ^ 85%-88% of safety issues were remediated (issuu.com)
- ^ through the Rana Plaza Arrangement (ranaplaza-arrangement.org)
- ^ one-third of all the garment factories in Bangladesh (pages.stern.nyu.edu)
- ^ Rehman Asad/NurPhoto via Getty Images (www.gettyimages.com)
- ^ spent 10% of its income on clothing (www.kqed.org)
- ^ makes barely 18 cents (theconversation.com)
- ^ be closer to $10 (www.cnn.com)
- ^ a very appealing alternative (qz.com)
- ^ the country’s export total (bgmea.com.bd)
- ^ employs 4 million people (www.bsr.org)
- ^ reduced poverty (dspace.bracu.ac.bd)
- ^ empowered women (doi.org)
- ^ subcontract part of the production to smaller factories (issuu.com)
- ^ exploitative labor practices (www.reuters.com)
- ^ Munir Uz Zaman/AFP via Getty Images (www.gettyimages.com)
- ^ scrutiny of labor conditions (www.degruyter.com)
- ^ unwilling or unable to enforce laws (www.npr.org)
Authors: Ravi Anupindi, Professor of Technology and Operations, University of Michigan