When Faith Becomes a Weapon: Rebuilding Trust in a Divided Society
- Written by Mark J. Chironna, PhD.
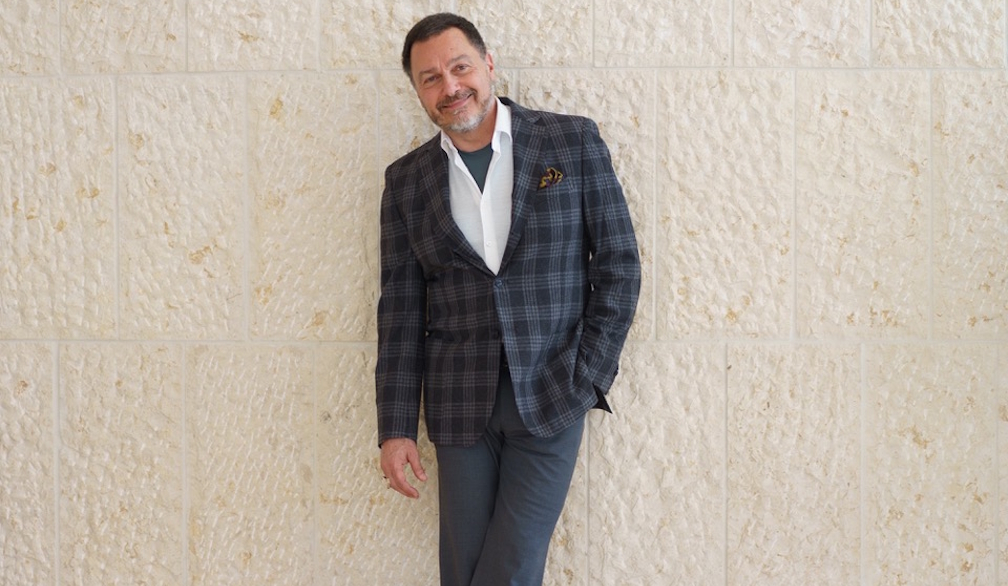
Faith is meant to provide guidance, meaning, and a sense of connection. Yet, when faith is weaponized, manipulated and exploited as a tool to achieve political dominance, fuel cultural conflict, and deepen social divisions, we cannot call it genuine faith. This weaponization occurs when deeply held religious convictions are stripped of their spiritual essence and repurposed as ammunition in ideological battles. Instead of serving as a source of compassion or a unifying moral vision, faith becomes a means to an end, often wielded aggressively against perceived adversaries.
We live in a cultural moment marked by sharp divisions, mutual suspicion, and the slow erosion of civil discourse. Trust across political and social boundaries has fractured, only 34 percent of Americans believe “most people can be trusted,” down from 46 percent in 1972.i This decline in social trust reflects deeper anxieties, economic, cultural, and technological, that shape how communities now define themselves more by who they oppose than what they share.
The RAND Corporation highlights another layer of this fracture. Its Truth Decay research describes how factual disagreement, opinion masquerading as fact, and fading trust in institutions have combined to erode healthy public conversation. The consequences are severe: civic paralysis, disengagement, and an unmistakable “erosion of civil discourse”.ii It’s not just that we argue more. We argue worse, with less shared reality to anchor those disagreements.
The 2019 Pew survey confirms what RAND observes: public confidence in fellow citizens and in government is waning. When people begin to believe that those on the other side are either uninformed or dangerous, our common ground starts to crumble.iii
This divisive atmosphere doesn’t just weaken our civic fabric; it also undermines the very faith traditions it claims to champion. When trust evaporates, when shared values are replaced by suspicion, the compassionate public witness of faith loses its power.
This weaponization should be deeply troubling to all concerned citizens. When religion is harnessed to political or social agendas, something vital is lost. Faith's potential to foster empathy, humility, and healing diminishes, replaced by a moral absolutism that fuels division rather than reconciliation.
Psychologist Jonathan Haidt provides useful insight into how morality shapes these divisions. He highlights that humans across cultures construct their moral understanding on a foundational recognition that causing harm is fundamentally wrong. Yet Haidt also emphasizes that morality involves more than harm and fairness alone, cultural learning fundamentally shapes what we consider morally important. Moral reasoning, he explains, is often a post hoc justification of our intuitive feelings, particularly those related to disgust and disrespect, rather than an impartial search for truth. In other words, morality emerges as an interplay between innate intuition and social learning.iv
This insight clarifies how easily faith can be weaponized: by activating intuitive feelings of disgust or disrespect toward opponents, faith becomes a powerful tool for polarization rather than unity. My aim here is to explore how and why this happens, and to consider a path toward reclaiming faith as a source of shared human flourishing rather than conflict.
Understanding morality as this complex mix of intuition, cultural conditioning, and social learning helps us grasp how easily religion can be co-opted for divisive ends. If moral reasoning often follows intuitive, emotional reactions rather than guiding them, it becomes clearer why religious beliefs, deeply rooted in both culture and emotion, are especially susceptible to manipulation.
When religious identity is fused to political or cultural loyalty, differences become threats rather than invitations for dialogue or understanding. Religious teachings about right and wrong become polarized absolutes, making compromise or even respectful disagreement increasingly difficult. In short, faith no longer guides morality toward compassion or empathy; instead, it is wielded defensively, to protect cultural or political tribes at all costs.
How did we get here, to this place where something meant to bring connection instead fuels suspicion and hostility? And what can we do about it? To answer these questions, we first need to examine how faith is strategically weaponized today, how it happens, who benefits, and why it works so effectively.
America’s divisions are rooted in moral, psychological, and historical realities. Religion, ideally a source of unity and compassion, is often drawn into conflicts as a proxy for political, cultural, and tribal identities. The result is stark division and mistrust.
Haidt contends that morality is not primarily about logical reasoning or abstract fairness. Instead, moral views often reflect intuitive emotions, particularly feelings of disgust, disrespect, or threat. Humans first feel, then construct moral arguments to justify those feelings. Moral reasoning, Haidt argues, frequently serves as a "post hoc justification" of intuitive emotional reactions.v
This psychological insight aligns closely with Rowan Williams' theological reflections on choice and desire. Williams observes how contemporary culture typically views freedom and morality through the lens of consumer choice, as isolated acts disconnected from deeper desires. He critiques this superficial notion of freedom as simply “a series of disconnected, fractured acts of choosing.”vi Rather than reflecting genuine freedom or moral depth, this kind of choosing emerges primarily from surface-level impulses or anxieties.
Williams instead highlights that authentic moral life arises from a profound awareness of our deeper desires and the direction toward which our lives are oriented. True morality involves patiently discerning "the deepest rhythms of our life," finding the context "in which we will grow as God means us to," rather than impulsively asserting our momentary preferences.vii For Williams, the root of genuine morality is love, understood not merely as "doing good" but as "a deep contemplative regard for the world, for humanity... and for God.”viii
Media today often fragments us instead of connecting us. Algorithms prioritize what keeps us scrolling, what shocks, enrages, or confirms what we already believe. This dynamic creates online echo chambers, where we see more of our own views and little of others’. A growing body of research confirms this cycle:
A study titled The Echo chamber–driven Polarization on Social Media describes echo chambers as “insulated online spaces where individuals are exposed primarily to likeminded perspectives,”ix with recommendation systems amplifying these silos and reinforcing extreme views.
RAND’s Truth Decay report highlights how algorithm-driven media, mixed with cognitive bias and political polarization, is eroding public discourse. These shifts pull facts apart from opinions and damage trust in institutions, ultimately leading to weakened civic engagement and higher social distrust.x
Recent research strengthens these findings: platforms with algorithmic feeds, like “X”, often guide users into denser, more insular communities than those who follow content through personal networks. Although some studies debate how much algorithms directly cause polarization, the consensus is clear, these systems intensify existing divides.xi
The result is not just misinformation; it’s a fractured public that lives in alternate realities. As people retreat into their own digital bubbles, shared truth becomes rare. This atmosphere breeds fear, suspicion, and misidentification of opponents not just as wrong, but as threats, a fertile ground for weaponized narratives tied to culture, religion, or identity.
Addressing this fragmentation means refreshing our public spaces, especially spaces of faith. If faith communities are to repair our civic bonds, we must rebuild shared platforms for honest conversation. We must design media environments, digital or physical, where facts are honored, differences are heard, and trust can grow again.
The phrase “Christian nationalism” is often used as though it describes a single, monolithic movement. The reality is far more complex. Academic research reveals a spectrum of belief, ranging from mild cultural affinity to full ideological commitment.
Sociologists Andrew Whitehead and Samuel Perry show that self-identified Christians in America fall into four categories regarding national identity and religion: Ambassadors (fully committed to Christian nationalism, roughly 20%); Accommodators (sympathetic, about 32%); Resisters and Rejecters (who oppose or reject Christian nationalist views, totaling around 48%).xii
These findings mean most Christians do not endorse the most explicit forms of Christian nationalism.
Whitehead and Perry define Christian nationalism as “a cultural framework that blurs the distinctions between Christian identity and American identity,” often combining conservative political views, religious imagery, and moral narratives in public life.xiii Understanding this makes clear that it isn’t simply religious belief, but a specific fusion of faith with civic and national identity.
Groups such as Christians Against Christian Nationalism, led by Amanda Tyler of the Baptist Joint Committee, show how many Christian communities resist this ideology. They “loudly denounce Christian nationalism as a distortion of our faith and a divisive force in our country,” positioning themselves in defense of democratic pluralism and religious freedom.xiv
Treating all faith-based civic action as Christian nationalism alienates those Christians who affirm their faith daily while rejecting exclusionary, authoritarian narratives. Holding space for that distinction is crucial, it allows us to challenge the misuse of religion while honoring sincere, faith-informed civic participation.
Reclaiming faith from its political captivity begins with acknowledging that faith itself is fundamentally relational. It thrives when grounded in humility, empathy, and openness to others—not suspicion, hostility, or the defensive posture of tribalism. If we genuinely desire healing and unity, we must confront the temptation to reduce faith to a tool for power. Instead, let us reaffirm faith as an invitation to deeper connection, not just with God, but with each other.
Faith traditions across time offer us guidance toward shared flourishing. The Hebrew prophets envisioned justice and mercy flowing through community life. The teachings of Jesus compel love of neighbor, and even enemy, as the hallmark of genuine belief. In our cultural moment, reclaiming these foundations becomes both spiritually necessary and socially transformative.
This effort demands courage: the courage to refuse easy answers that demonize others; the courage to listen generously, even when it is uncomfortable; and the courage to create spaces—digital, spiritual, communal, where dialogue, compassion, and respect can flourish again.
In a pluralistic democracy, we choose every day to see beyond labels, beyond our differences in belief or practice, to honor one another simply as fellow human beings. At the heart of our shared humanity is a dignity that no religious, cultural, or ideological boundary can erase. Loving our neighbor means granting each person the respect, kindness, and openness that reflects the image of God in everyone, regardless of their faith, or even the absence of it. When we practice this kind of genuine hospitality, our democracy is strengthened, becoming a space where diverse voices flourish together, each enriching the other, and where faith itself can embody its deepest calling: to love without conditions, embrace without fear, and heal without reservation.
The path forward may not be quick or simple, but it remains deeply hopeful. By choosing authenticity over manipulation, dialogue over division, and humility over hostility, we can rediscover faith’s true potential: not as a weapon, but as a wellspring of renewal, unity, and shared humanity.
Written by Mark J. Chironna, PhD. - https://www.markchironna.com/
Bishop Mark J. Chironna PhD
Church On The Living Edge
Mark Chironna Ministries
The Issachar Initiative
Order of St. Maxmius
United Theological Seminary, Visiting
Professor, Co-director, House of Pentecostal Studies
Dr. Mark Chironna is a public scholar, executive and personal coach, and thought leader with five decades of experience in leadership development, cultural analysis, and future-focused strategies. With advanced degrees in Psychology, Applied Semiotics and Futures Studies, and Theology, he brings a unique interdisciplinary approach to helping individuals and organizations navigate complexity, unlock potential, and craft innovative solutions.
As a Board Certified Coach with over 30,000 hours of experience, he empowers leaders and teams to thrive through resilience, foresight, and actionable strategies. Passionate about human flourishing, he integrates psychological insight and cultural trends to inspire growth and transformation.
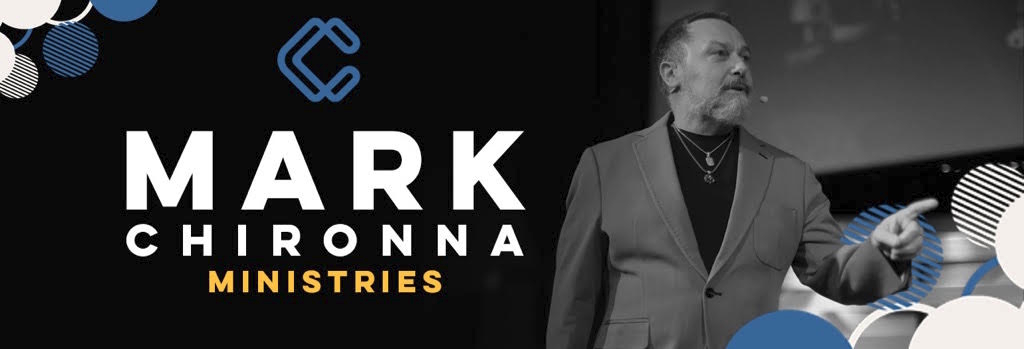
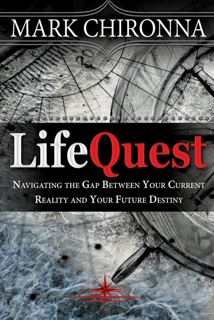