Boeing door plug blowout highlights a possible crisis of competence − an aircraft safety expert explains
- Written by Daniel Kwasi Adjekum, Assistant Professor of Aviation, University of North Dakota
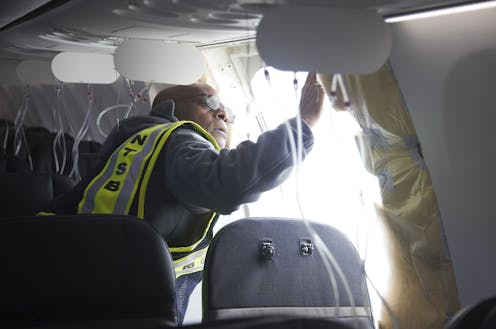
In the wake of the in-flight blowout of the side of a Boeing 737 Max 9[1], federal regulators have grounded planes and are stepping up scrutiny of Boeing’s manufacturing process.
The Jan. 5, 2024, explosive decompression after takeoff was related to a component called a “door plug” being ejected from the fuselage of the aircraft. This was after three prior flights of that plane[2] had registered warning signals about cabin pressurization. The National Transportation Safety Board is investigating that incident.
In addition, the Federal Aviation Administration has launched an investigation into Boeing’s manufacturing process. Other incidents have raised concerns about other 737 Max aircraft – not just fatal crashes in 2018 and 2019[3], but more recent examples of bolts or other fittings or fasteners[4] not being up to standards.
The Conversation U.S. asked Daniel Kwasi Adjekum[5], an aviation safety expert and professor of aviation at the University of North Dakota, to explain the significance of the incident, the government’s response and what it all means for the flying public.
Why is Boeing – not the airline – responsible for the door plug being secure?
Under U.S. federal requirements, the number of occupants in an aircraft and the seating arrangements determine the number and placements of emergency exit doors[6]. Airplane manufacturers build fuselages with enough openings to accommodate all the doors that might be needed. If airlines choose to use the highest-density seating arrangements, they need to use all of the openings for actual exit doors. But not all airlines pack the seats in that tightly; on those planes, some emergency doors are not needed. Those spaces are filled by door plugs.
In the case of the Boeing 737 Max 9 aircraft, the door plugs are fitted by Spirit AeroSystems in Wichita, Kansas, which is the supplier of the airframe to Boeing. The final assembly of the aircraft is carried out at the Boeing plant in Renton, Washington. Quality control checks are done at Spirit AeroSystems, and then another round of quality checks is done by Boeing. These include a high-pressure test to ensure that the cabin can be pressurized safely and to ensure the integrity of the fuselage and pressure bulkheads.
Normally, the plugs are not removed during those tests at the Boeing facility, though they are checked to ensure they are correctly aligned with the rest of the fuselage. Overall, it is Boeing’s responsibility, as the original equipment manufacturer, to ensure the components conform to the FAA’s design, manufacturing, installation and performance requirements.
Do the airlines have any reason to inspect the bolts that fasten the plugs in place?
Under normal circumstances, once they are delivered and initially inspected, door plugs and their components are not adjusted by the airline maintenance team, though their integrity is checked as part of stipulated maintenance checks. Records from Alaska Airlines suggest that on previous flights before this incident, pilots had received cockpit alerts[7] indicating a failure of the aircraft’s cabin auto-pressurization system.
In a situation like that, where there are suspected cabin pressurization issues, it may be possible for airline maintenance crews to check all cabin doors, windows, seals and potentially door plugs as part of a thorough troubleshooting process, but they would be subject to Boeing’s procedures for inspecting a door plug.
What do FAA investigations involve?
The design, testing, certification and approval process for any new aeronautical product is supposed to be in compliance with strict legal and FAA regulatory standards[9].
As part of the investigations in this case, the FAA will review the engineering and manufacturing processes[10] for the Boeing 737 Max 9, including the processes for vendors and suppliers, to determine if those standards were met. The FAA will review documentation[11] on quality control and assurance processes and analyze components.
The FAA has said it is considering bringing in a third party[12] to conduct an audit of the engineering and manufacturing processes for the Boeing 737 Max 9. The findings and recommendations from the National Transportation Safety Board incident investigation[13] may also provide valuable information.
How do airlines deal with having so many airplanes that are now out of service pending their various inspections?
With all these aircraft grounded, you need hangars and parking places for temporary storage. And it costs. In the U.S. alone we’re talking about 171 airplanes[14] on the ground.
That is a huge financial loss to airlines, which are otherwise benefiting from a surge in air service demand and increased passenger interest[15].
Airlines’ fleet plans – entailing which aircraft they send on which routes and in what sequence – will be disrupted. Some high-traffic routes normally served by these aircraft will have to be done by other aircraft with limited seat and load capacities. That can reduce expected revenue.
The current scenario will also affect flight crew scheduling. Some crew members may have their work hours reduced or eliminated, at least for a period of time.
Once investigators have determined what went wrong, and how to fix whatever it was, that corrective action will also take a lot of maintenance work, in addition to the normal maintenance work for keeping the rest of the planes fit for flying.
It also appears that the FAA may want to inspect each plane[16] after it is fixed before certifying it to return to service. That will require significant amounts of inspection time.
How does an airliner manufacturer regain public confidence? Have other companies dealt with this before?
In the 1970s, McDonnell Douglas had airworthiness issues with the DC-10 aircraft. Its cargo door sometimes opened midflight[18], resulting in injuries and fatalities[19].
The incidents were a big public relations problem for McDonnell Douglas, but using recommendations from the accident investigations, the company managed to redesign the door.
In the 1990s, ATR had its own issues with the ATR 72’s de-icing system[20]. The company completely redesigned the system and gradually came back into the market.
Airbus has also faced similar challenges: Some Airbus A320neos using Pratt and Whitney 1100G engines[21] had vibration problems that required review with engine manufacturers and regulators.
Most aircraft manufacturers are aware technical issues can surface after deploying a product into the market. That is why it’s important for them to get continuous feedback from operators on reliability and safety.
Boeing’s situation is difficult in part because of previous problems with other 737 Max models, including fatal crashes in 2018 and 2019. In my view, the company will need a lot of transparency and leadership to address these hits to its reputation.
To me, the company’s best chance for surviving this crisis would be to take full responsibility for what has happened and avoid blaming its suppliers. Boeing could involve airline executives, pilots, engineers, cabin crew, media and others in a wide-ranging discussion of quality and safety. If Boeing could win the confidence of these key stakeholders who operate its aircraft, that could help reestablish credibility for its brand with the traveling public.
In early 2023, Boeing was planning to ramp up production of the 737 Max line[22]. My suggestion would be that the company make product safety and quality an immediate priority and worry later about maximizing production goals and profits, after Boeing’s reputation is restored.
References
- ^ in-flight blowout of the side of a Boeing 737 Max 9 (www.cnn.com)
- ^ three prior flights of that plane (apnews.com)
- ^ fatal crashes in 2018 and 2019 (theconversation.com)
- ^ bolts or other fittings or fasteners (www.bbc.com)
- ^ Daniel Kwasi Adjekum (scholar.google.com)
- ^ number and placements of emergency exit doors (www.ecfr.gov)
- ^ pilots had received cockpit alerts (apnews.com)
- ^ NTSB via AP (newsroom.ap.org)
- ^ legal and FAA regulatory standards (www.ecfr.gov)
- ^ review the engineering and manufacturing processes (www.npr.org)
- ^ FAA will review documentation (www.seattletimes.com)
- ^ considering bringing in a third party (www.faa.gov)
- ^ National Transportation Safety Board incident investigation (www.npr.org)
- ^ 171 airplanes (www.newsweek.com)
- ^ surge in air service demand and increased passenger interest (edition.cnn.com)
- ^ FAA may want to inspect each plane (www.faa.gov)
- ^ Mathieu Lewis-Rolland/Getty Images (www.gettyimages.com)
- ^ cargo door sometimes opened midflight (www.smithsonianmag.com)
- ^ fatalities (mitpressbookstore.mit.edu)
- ^ ATR 72’s de-icing system (www.faa.gov)
- ^ Airbus A320neos using Pratt and Whitney 1100G engines (simpleflying.com)
- ^ ramp up production of the 737 Max line (www.reuters.com)
Authors: Daniel Kwasi Adjekum, Assistant Professor of Aviation, University of North Dakota